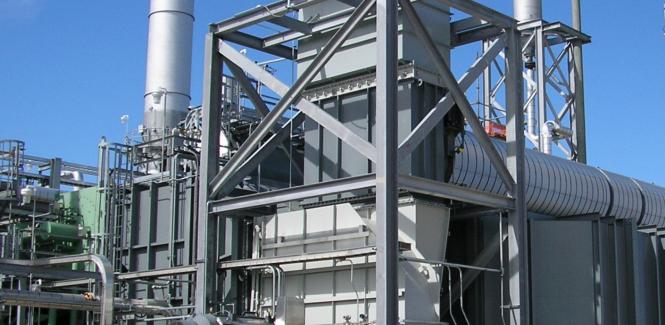
Forced Draft Fans
The Forced Draft Fan (FD Fan) is a fundamental part of most boiler systems and is the element responsible for creating draft inside of the boiler. The FD Fan provides the pressure and flow required to push air, fuel, and the resulting flue gases created from combustion through the boiler, catalysts, economizer, FGR ductwork, and stack. FD Fans are manufactured in several different arrangements, depending on the size of the boiler. Auxiliary pieces that often accompany the FD Fan include Inlet Silencers, FGR Mixing Boxes, Dampers, and Damper Actuators. FD Fans are designed to be driven by a Steam Turbine or an Electric Motor with an optional Variable Frequency Drive (VFD). Occasionally, the FD Fan is designed to use both of these prime movers in conjunction.